Pipe Nipples
Stainless Steel Pipe Nipples
Black Steel Pipe Nipples
Galvanized Pipe Nipples
King Nipples
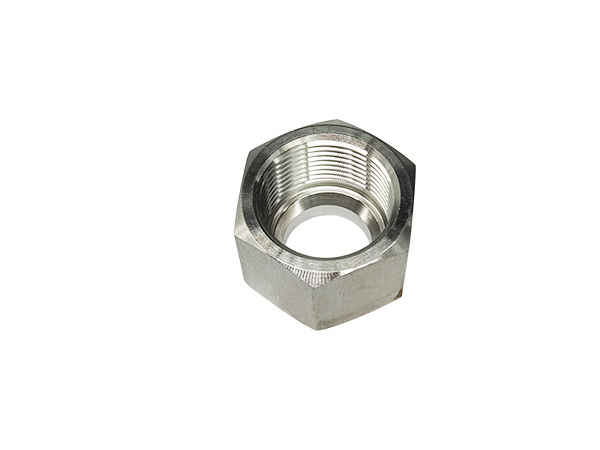
Seamless Threaded Pipe Fittings
The welding process of seamless threaded pipe fittings requires comprehensive consideration of various factors such as pipe material,pipe type,and working conditions.The following is a detailed introduction for you:
Preparation before welding
Material confirmation
Check the materials and specifications of seamless threaded fittings and welding materials(welding rods,welding wires,etc.)to ensure that they match and meet the design requirements.For example,when welding seamless threaded carbon steel fittings,E43 series welding rods can usually be used;When welding stainless steel fittings,corresponding stainless steel welding rods should be used,such as E308 welding rods for welding 304 stainless steel fittings.
Check the quality certification documents of the pipe fittings and welding materials,inspect the surface of the pipe fittings for defects such as cracks and sand holes,and check the welding materials for moisture,deterioration,and other conditions.
Groove processing
According to the thickness and welding requirements of the pipe fittings,mechanical processing(such as lathe,milling machine)or thermal cutting(such as plasma cutting)methods are used to process the groove.Common groove forms include V-shaped,U-shaped,X-shaped,etc.For example,when the thickness of the pipe is small,a V-shaped groove can be used;When the thickness is large,U-shaped or X-shaped grooves can be used to reduce the amount of welding filling.
The surface of the processed groove should be smooth and free of impurities such as scale,oil,rust,etc.Use tools such as angle grinders to polish a certain range on both sides of the groove until a metallic luster is exposed.
Pipe cleaning
Clean the welding parts and adjacent areas of the pipe fittings with organic solvents such as acetone or alcohol to remove impurities such as oil and moisture,in order to ensure welding quality.
Debugging of welding equipment
According to the welding process requirements,adjust the parameters such as current,voltage,and welding speed of the welding equipment.For example,when manual arc welding carbon steel,the current size can be selected according to the diameter of the welding rod.Generally,for welding rods with a diameter of 3.2mm,the welding current can be between 100-130A.
Check the performance and safety of welding equipment to ensure its normal operation.
Welding process selection
Manual arc welding(SMAW)
Features:The equipment is simple and flexible to operate,suitable for welding in various positions,and has strong adaptability to the construction site environment.But the welding efficiency is relatively low,and the welding quality is greatly affected by the welder's technical level.
Applicable situation:It is commonly used for welding seamless threaded pipe fittings in small batches,irregular positions,or on-site maintenance,such as pipeline connection welding in some construction sites.
Gas shielded welding(GMAW and GTAW)
GMAW(Gas Metal Arc Welding)
Features:High welding efficiency,good weld quality,and the ability to achieve automated or semi automated welding.But there are high requirements for the welding environment,and windproof measures need to be taken.
Applicable situation:Suitable for welding large-scale production and thicker pipe fittings,such as seamless threaded pipe fittings produced on factory assembly lines.According to the different shielding gases,it can be divided into carbon dioxide gas shielded welding(CO₂welding)and mixed gas shielded welding(such as Ar+CO₂).
GTAW(non melting electrode gas shielded welding,also known as tungsten inert gas welding)
Features:Beautiful weld formation,high welding quality,suitable for welding various metal materials,especially in situations where high welding quality is required.But the welding speed is slow and the penetration depth is shallow.
Application:Commonly used for welding seamless threaded pipe fittings made of stainless steel,non-ferrous metals,and other materials,as well as for bottom welding with strict requirements for weld quality.
Submerged arc welding(SAW)
Features:High welding efficiency,stable weld quality,deep penetration,and good working conditions.But the equipment is more complex and has poor flexibility,generally suitable for welding long welds in flat positions.
Applicable situation:Suitable for welding large diameter,thick walled seamless threaded pipe fittings,such as welding fittings in some large pipeline projects.
Welding process control
Preheating(optional)
For some materials with poor weldability(such as high carbon steel,alloy steel,etc.)or thick pipe fittings,preheating is required before welding.Preheating can reduce welding stress and prevent crack formation.The preheating temperature is determined based on the material and the thickness of the pipe fittings.For example,when welding 15CrMo alloy steel pipe fittings with a large thickness,the preheating temperature may need to reach 150-200℃.
The preheating method can be flame heating,electric heating,etc.The heating should be uniform to ensure that the entire pipe reaches the preheating temperature.
Welding operation
Arc ignition:When manually arc welding,the scratch method or direct strike method can be used,but attention should be paid to avoiding arbitrary arc ignition on the surface of the pipe to avoid damaging the surface of the pipe.When starting the arc in gas shielded welding,it is necessary to ensure that the shielding gas is delivered in advance to eliminate the air in the welding area.
Welding speed:Maintain an appropriate welding speed to avoid defects such as poor fusion and porosity caused by too fast a speed.If the speed is too slow,the weld seam will widen and deformation will increase.The welding speed should be adjusted according to the welding process parameters and weld requirements.
Welding layers:For thicker pipe fittings,multiple layers and multiple passes of welding are required.The thickness of each weld seam should not be too thick,generally controlled at 3-5mm.After each layer of welding is completed,the welding slag should be cleaned up in a timely manner,and the quality of the weld seam should be checked.If there are defects,they should be dealt with in a timely manner before proceeding to the next layer of welding.
Swinging method:During the welding process,appropriate swinging methods can be used according to the width and requirements of the weld seam,such as straight lines,crescent shapes,sawtooth shapes,etc.The swing amplitude should be uniform to ensure consistent weld width and good fusion.
Interlayer temperature control
When welding multiple layers and passes,it is necessary to control the interlayer temperature.Excessive interlayer temperature can cause coarsening of weld grains and reduce the mechanical properties of the weld;If the temperature is too low,it may cause cracks to form.The interlayer temperature should generally be maintained within a range similar to the preheating temperature.
Post weld treatment
Post heating(optional)
For some materials that are prone to delayed cracking(such as high-strength alloy steel),post welding heating is required.Post heating can accelerate the escape of hydrogen from the weld seam,reduce welding residual stress,and prevent the occurrence of delayed cracks.The post heating temperature and time are determined according to the material and welding process.Generally,the post heating temperature is between 200-350℃,and the insulation time is 0.5-2 hours.
Weld cleaning
After welding,use tools such as slag hammers and wire brushes to clean the surface of the weld seam of impurities such as welding slag and spatter,making the surface of the weld seam flat and smooth.
Heat treatment(optional)
For some pipe fittings that require high mechanical properties of the weld seam,post weld heat treatment such as annealing,normalizing,tempering,etc.is required.Heat treatment can eliminate residual stresses in welding,improve the microstructure and properties of welds and heat affected zones.The heat treatment process parameters are determined based on the material of the pipe fittings and design requirements.
quality testing
Appearance inspection:Check whether there are cracks,pores,slag inclusions,undercutting and other defects on the surface of the weld seam,and whether the dimensions of the weld seam such as excess height and width meet the requirements.
Non destructive testing:According to design requirements and relevant standards,non-destructive testing is carried out on welds,such as ultrasonic testing(UT),radiographic testing(RT),magnetic particle testing(MT),penetrant testing(PT),etc.,to detect whether there are defects inside the weld.
Mechanical performance test(optional):For important welded structures,mechanical performance tests such as tensile test,bending test,impact test,etc.may be required to verify whether the mechanical properties of the weld meet the design requirements.
What should I do if the stainless steel joint leaks?
Stainless steel joints are a common type of pipeline connection,which are widely used in in ...
2025-01-07
Several common problems in the use of stainless steel joints
With the continuous development of stainless steel joint technology and enterprises, stainl ...
2025-01-07
How to deal with the phenomenon of stainless steel joints shining?
A simple stainless steel joint is dipped in toothpaste or vinegar with a cotton cloth, and ...
2025-01-07
How is the hardness of stainless steel threaded fittings measured?
Stainless steel threaded fittings are generally measured by three hardness indicators:Brine ...
2025-01-07