Pipe Nipples
Stainless Steel Pipe Nipples
Black Steel Pipe Nipples
Galvanized Pipe Nipples
King Nipples
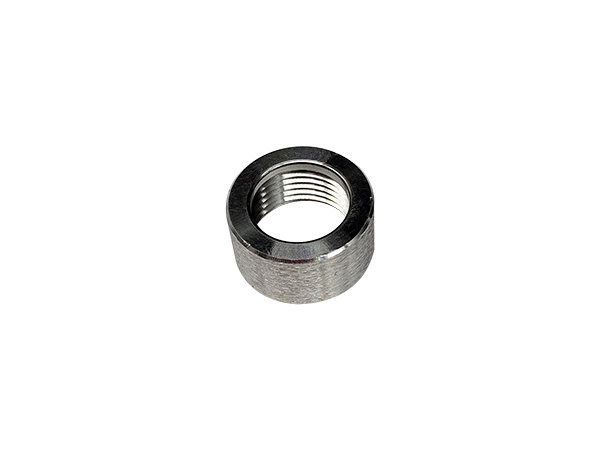
Seamless Threaded Pipe Fittings
In the welding process of seamless threaded pipe fittings,the welding position has a significant impact on the difficulty of welding operations and the quality of weld seams.The common welding positions include flat welding,vertical welding,horizontal welding,and overhead welding.The following is a detailed introduction for you:
Flat welding
characteristic
Easy to operate:Flat welding is the easiest welding position to operate,and welders can easily control the movement trajectory and molten pool shape of the welding rod or wire during welding.Due to the favorable effect of gravity on droplet transition,the liquid metal in the molten pool can flow smoothly,resulting in better weld formation and relatively fewer defects such as porosity and slag inclusion.
High welding efficiency:Due to the low operational difficulty,welders can use larger welding currents and faster welding speeds to improve welding efficiency,making it suitable for large-scale production and welding of long welds.
Applicable situation:Widely used for welding various types of seamless threaded pipe fittings,especially in situations where welding quality and production efficiency are high requirements.For example,in factory assembly line production,flat welding is the preferred welding position for horizontally placed pipe fittings.
Operation points
Keep the welding rod or wire perpendicular or slightly inclined to the surface of the workpiece,generally at an angle between 5°and 15°,to ensure penetration depth and weld width.
Control welding speed and welding current to avoid problems such as weld seam width,height,or burn through.Usually,the welding current can be slightly higher during flat welding,but it should be adjusted reasonably according to the thickness of the welded part and the diameter of the welding rod.
Vertical welding
characteristic
Difficulty in operation:During the vertical welding process,the liquid metal in the molten pool is prone to falling due to gravity,resulting in difficulty in forming the weld seam and the occurrence of defects such as undercutting and weld bead.Therefore,welders need to possess high operational skills and rich experience.
High requirements for weld quality:In order to ensure the quality of the weld,appropriate welding processes and operating methods need to be adopted,such as controlling the welding current,using short arc welding,and appropriate strip transportation methods,to prevent liquid metal from falling down and ensure good weld formation.
Applicable situation:Commonly used for vertical connection of pipe fittings or welding seams on vertical surfaces,such as the connection welds of vertical pipelines in building structures.
Operation points
Using smaller welding currents and shorter arcs to reduce the volume and heat input of the molten pool and prevent liquid metal from falling.
The transportation method can be triangular,serrated,etc.,and the shape of the molten pool and the width of the weld can be controlled by appropriate swinging.When welding upwards,attention should be paid to the feeding speed and angle of the welding rod or wire,so that the molten droplet can smoothly transition into the molten pool.
Horizontal welding
characteristic
Difficulty in controlling the molten pool:During horizontal welding,the liquid metal in the molten pool is prone to flow downward under the combined action of gravity and arc blowing force,resulting in defects such as undercutting on the upper side of the weld and weld bead on the lower side.Therefore,there is a high demand for controlling the melt pool.
Strict welding process requirements:it is necessary to choose appropriate welding parameters and strip transportation methods to ensure the quality of the weld formation.At the same time,attention should be paid to controlling the welding speed to avoid welding seams that are too wide or too narrow.
Applicable situation:Suitable for welding at the intersection of horizontal and vertical planes of pipe fittings,such as the connection weld between pipes and vertical supports.
Operation points
Using smaller welding currents and faster welding speeds to reduce heat input into the melt pool and flow of liquid metal.
When transporting the welding rod,the welding rod or wire should be inclined towards the uphill end of the weld seam,so that the molten droplet transitions to the upper side of the weld seam,while swinging appropriately to ensure good fusion on both sides of the weld seam.
Upward welding
characteristic
The most difficult operation is upward welding,which requires the welder to operate in an upward position.The liquid metal in the molten pool is easily dropped due to gravity,making it extremely difficult to form and control the quality of the weld seam.The welder's skill level and physical fitness are required to be high.
Strict welding quality requirements:Due to the difficulty of operation,defects such as porosity,slag inclusion,and lack of fusion are prone to occur during upward welding.Therefore,it is necessary to strictly control the welding process parameters and operating methods to ensure the quality of the weld seam.
Applicable situations:In some special installation positions or maintenance work,overhead welding may be encountered,such as welding seams at the bottom of pipelines,overhead welding seams in narrow spaces inside equipment,etc.
Operation points
Adopting the minimum welding current and shortest arc to reduce the volume and heat input of the molten pool and prevent liquid metal from falling.
The strip transportation method should be smooth and uniform,and crescent shaped,circular and other strip transportation methods can be used to control the shape of the molten pool and the width of the weld seam through appropriate swinging.At the same time,attention should be paid to observing the condition of the molten pool and adjusting welding parameters and strip transport speed in a timely manner.
What should I do if the stainless steel joint leaks?
Stainless steel joints are a common type of pipeline connection,which are widely used in in ...
2025-01-07
Several common problems in the use of stainless steel joints
With the continuous development of stainless steel joint technology and enterprises, stainl ...
2025-01-07
How to deal with the phenomenon of stainless steel joints shining?
A simple stainless steel joint is dipped in toothpaste or vinegar with a cotton cloth, and ...
2025-01-07
How is the hardness of stainless steel threaded fittings measured?
Stainless steel threaded fittings are generally measured by three hardness indicators:Brine ...
2025-01-07