Pipe Nipples
Stainless Steel Pipe Nipples
Black Steel Pipe Nipples
Galvanized Pipe Nipples
King Nipples
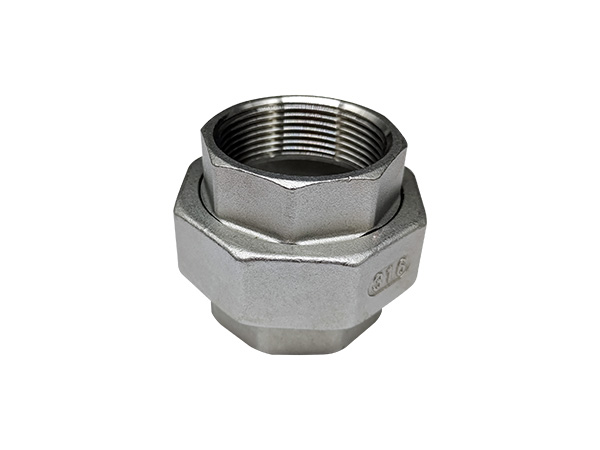
Galvanized Pipe Nipples
Galvanized steel pipe joint parts,including elbows,straight through fittings,internal teeth,bushings,reducers,tees,etc.
There are many key points to pay attention to in the production process of galvanized pipe joints,including raw material selection,mold design and manufacturing,production process control,quality inspection,etc.The following are the specific contents:
Raw material selection
Steel pipe material:High quality carbon steel or alloy steel that meets national standards should be selected to ensure good strength,toughness,and processability.It is necessary to check the quality certification documents of the materials,conduct chemical composition analysis and mechanical property testing on each batch of steel pipes to prevent insufficient joint strength or poor corrosion resistance due to material problems.
Quality of galvanized layer:The quality of galvanized layer directly affects the corrosion resistance of pipe joints.Choose galvanized pipes with uniform galvanized layer,strong adhesion,and thickness that meets the requirements.The corrosion resistance of the galvanized layer can be tested by methods such as salt spray testing,and the thickness of the galvanized layer can be measured using a magnetic thickness gauge to ensure that it is within the specified range.
Mold Design and Manufacturing
Design accuracy:Conduct precise mold design based on the specifications,shape,and usage requirements of galvanized pipe joints.Using computer-aided design(CAD)and computer-aided engineering(CAE)technologies,simulate and analyze the mold structure and forming process,optimize the mold design scheme,and ensure the quality of joint forming.
Manufacturing accuracy:High precision processing equipment and advanced processing technology are used to ensure the manufacturing accuracy of the mold.The dimensional tolerance and surface roughness of the mold should meet the design requirements,and the machining accuracy of key dimensions should be controlled within±0.01mm.The surface roughness should reach Ra0.8-Ra1.6μm to ensure the dimensional accuracy and surface quality of the joint.
Mold materials and heat treatment:Select suitable mold materials,such as Cr12MoV,H13,etc.,which have good wear resistance,toughness,and thermal stability.Reasonably heat treat the mold to improve its hardness and strength,and extend its service life.
Production process control
Cutting and cutting:According to the size requirements of the joint,suitable cutting equipment such as sawing machines,cutting machines,etc.are used to cut and cut galvanized pipes.When cutting,it is necessary to control the cutting speed and feed rate to ensure that the cutting surface is flat and the vertical deviation does not exceed±0.5mm,in order to prevent defects such as burrs and burrs.
Welding process:Choose appropriate welding methods such as manual arc welding,gas shielded welding,etc.,and strictly control the welding process parameters.Welding current,voltage,welding speed and other parameters should be adjusted according to factors such as pipe material and wall thickness to ensure welding quality.After welding,a visual inspection and non-destructive testing of the weld seam should be carried out,such as ultrasonic testing,radiographic testing,etc.,to promptly detect and eliminate defects such as porosity,slag inclusion,and cracks inside the weld seam.
Thread processing:Thread processing equipment such as lathes,tapping machines,etc.are used to process the threads of pipe joints.During processing,it is necessary to ensure that the accuracy,profile angle,and pitch of the thread meet the standard requirements.The surface of the thread should be smooth,free of burrs,and free of irregular teeth.Thread gauges can be used to inspect the processed threads to ensure thread quality.
Assembly process:During the assembly process,it is necessary to ensure that the installation positions of each component are accurate and the fitting clearances are appropriate.For joints with sealing requirements,it is necessary to ensure that the sealing components are installed in place and undamaged to ensure the sealing performance of the joint.After assembly,a comprehensive visual inspection and functional testing should be conducted to ensure that the joints meet the requirements for use.
Surface treatment and protection
Oil and rust removal:Before surface treatment,the oil,rust,and impurities on the surface of the pipe joint must be thoroughly removed.Chemical degreasing,acid pickling and rust removal methods can be used to ensure that the surface cleanliness reaches Sa2.5 level or above,providing a good foundation for subsequent galvanizing or painting treatments.
Galvanizing treatment:For pipe joints that require galvanizing,strict control of galvanizing process parameters such as plating solution composition,temperature,current density,time,etc.is necessary to ensure the quality of the galvanized layer.After galvanizing,passivation treatment should be carried out to improve the corrosion resistance and decorative properties of the galvanized layer.
Painting or protective coating:Paint or apply other protective coatings to the surface of pipe joints according to the usage environment and customer requirements.Before painting,the surface should be pre treated to ensure the adhesion of the coating.During the painting process,it is necessary to control the thickness and uniformity of the paint layer to avoid defects such as sagging,blistering,and missed coating.
Quality Inspection and Control
Dimensional accuracy testing:Measuring tools such as calipers,micrometers,coordinate measuring instruments,etc.are used to test the various dimensions of pipe joints to ensure that dimensional deviations are within the design requirements.Key dimensions should be inspected with emphasis,and the sampling ratio for each batch of products should not be less than 10%.If size deviations are found,production processes or molds should be adjusted in a timely manner.
Appearance quality inspection:Through visual inspection and magnifying glass tools,the appearance of pipe joints is inspected,mainly including surface roughness,galvanized layer or coating quality,whether there are cracks,sand holes,pores and other defects.The appearance quality should meet relevant standards and customer requirements.Products with appearance defects should be reworked or scrapped.
Performance testing:Conduct necessary performance tests on pipe joints,such as pressure tests,tensile tests,torque tests,etc.,to verify their mechanical and sealing properties.The test pressure for pressure testing should be determined according to the product's usage requirements,generally 1.5 times the working pressure,and the holding time should not be less than 5 minutes.Observe whether there is leakage,deformation,or other phenomena at the joint.
What should I do if the stainless steel joint leaks?
Stainless steel joints are a common type of pipeline connection,which are widely used in in ...
2025-01-07
Several common problems in the use of stainless steel joints
With the continuous development of stainless steel joint technology and enterprises, stainl ...
2025-01-07
How to deal with the phenomenon of stainless steel joints shining?
A simple stainless steel joint is dipped in toothpaste or vinegar with a cotton cloth, and ...
2025-01-07
How is the hardness of stainless steel threaded fittings measured?
Stainless steel threaded fittings are generally measured by three hardness indicators:Brine ...
2025-01-07