Pipe Nipples
Stainless Steel Pipe Nipples
Black Steel Pipe Nipples
Galvanized Pipe Nipples
King Nipples
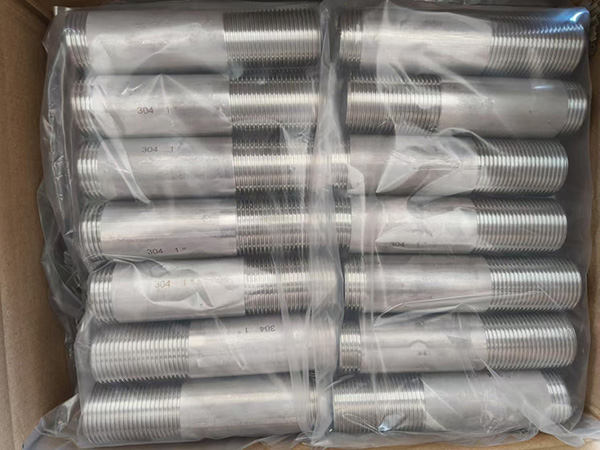
Welded Threaded Pipe Fittings
Welded Threaded Pipe Fittings are mainly used for pipeline connections,combining the firmness of welding with the convenience of threaded connections.The following is a detailed introduction to their production process:
Raw material preparation
Material selection:Choose suitable steel according to the requirements of pipe fittings and working environment,commonly including carbon steel,alloy steel,etc.Ensure that the raw materials have good weldability and mechanical properties,have quality certification documents,conduct sampling inspections on the raw materials,and check whether their chemical composition and mechanical properties meet the standard requirements.
Cutting and cutting:According to the size specifications of the pipe fittings,use sawing machines,cutting machines and other equipment to cut the raw materials into suitable lengths of pipe sections.The cutting size needs to be strictly controlled to ensure the accuracy of subsequent processing,and the allowable deviation is generally controlled within±0.5mm.
Thread processing
Thread forming:The end of the pipe section is threaded using equipment such as thread lathes and threading machines.According to the design requirements,determine the specifications(such as nominal diameter,pitch,tooth profile angle,etc.)and accuracy level of the thread.During the processing,it is necessary to ensure that the thread profile is complete and the surface smoothness meets the requirements,avoiding defects such as misalignment and broken threads.
Thread inspection:Use thread gauges and other tools to inspect the processed threads to ensure that the size and accuracy of the threads meet the standards.For unqualified threads,they need to be repaired or scrapped.
Welding preparation
Groove processing:To ensure welding quality,it is necessary to perform groove processing on the welding parts of the pipe section.The commonly used groove forms include V-shaped,U-shaped,etc.Choose the appropriate groove form and size according to the wall thickness and welding requirements of the pipe fittings.Groove processing can be carried out using mechanical processing(such as lathes,milling machines)or thermal cutting(such as plasma cutting)methods.After processing,impurities such as oxide scale and oil stains on the surface of the groove should be cleaned.
Welding material selection:Select suitable welding materials such as welding rods,welding wires,etc.based on the material and welding requirements of the pipe fittings.The chemical composition and mechanical properties of welding materials should match those of the base metal,and there should be quality certification documents.
Preheating before welding(optional):For some pipes with large thickness or poor weldability,preheating treatment is required before welding to reduce welding stress and avoid cracking.The preheating temperature and time are determined based on the material,thickness,and welding process of the pipe fittings.
Welding operation
Welding process selection:Choose the appropriate welding process based on the material,shape,and size of the pipe fittings,such as manual arc welding,gas shielded welding,submerged arc welding,etc.Different welding processes have different characteristics and applicability,and should be selected according to the actual situation.
Welding parameter determination:Determine appropriate welding parameters based on the requirements of the welding process and pipe fittings,such as welding current,voltage,welding speed,welding layers,etc.The selection of welding parameters directly affects the welding quality and needs to be optimized through experiments and experience.
Welding operation:During the welding process,it is necessary to strictly follow the welding process and operating procedures to ensure the quality of the weld formation.During welding,attention should be paid to controlling the welding speed and number of welding layers to avoid defects such as porosity,slag inclusion,and incomplete penetration.At the same time,attention should be paid to the welding sequence and direction to reduce welding deformation.
Heat treatment(optional)
Stress relief annealing:For some pipe fittings that are subjected to high pressure or have high requirements,stress relief annealing treatment is required after welding to eliminate welding stress,improve the reliability and service life of the pipe fittings.The annealing temperature and time are determined based on the material and size of the pipe fittings.
Normalizing or quenching tempering:For some pipe fittings that require increased strength and hardness,normalizing or quenching tempering treatment can be carried out to improve the mechanical properties of the pipe fittings.
quality testing
Appearance inspection:Inspect the appearance of welded threaded fittings,and ensure that the weld seam is flat,smooth,and free of defects such as cracks,pores,and slag inclusions.The surface of the pipe fittings should be free of obvious scratches,dents,and other defects.
Dimensional inspection:Use measuring tools to measure the dimensions of pipe fittings,including pipe diameter,wall thickness,length,thread size,etc.,to ensure that the dimensions meet the design requirements.
Non destructive testing:Non destructive testing methods(such as ultrasonic testing,radiographic testing,magnetic particle testing,etc.)are used to inspect the welds and check for any defects inside the welds.
Pressure test:Conduct a pressure test on the pipe fittings to check their sealing performance and pressure resistance.The test pressure and time are determined according to the usage requirements and standards of the pipe fittings.
surface treatment
Rust removal:Shot blasting,sandblasting and other methods are used to remove rust from the surface of pipe fittings,removing impurities such as oxide scale and rust,and improving surface quality.
Anti corrosion treatment:According to the usage environment and requirements of the pipe fittings,anti-corrosion treatment is carried out on the surface of the pipe fittings,such as painting,galvanizing,spraying,etc.,to improve the corrosion resistance of the pipe fittings.
Packaging and storage
Packaging:Qualified welded threaded pipe fittings shall be packaged using packaging materials such as plastic bags,paper boxes,and wooden boxes to prevent damage during transportation and storage.
Storage:Store the packaged pipe fittings in the warehouse,classify them according to specifications,models,batches,etc.,and label them properly for management and retrieval.
What should I do if the stainless steel joint leaks?
Stainless steel joints are a common type of pipeline connection,which are widely used in in ...
2025-01-07
Several common problems in the use of stainless steel joints
With the continuous development of stainless steel joint technology and enterprises, stainl ...
2025-01-07
How to deal with the phenomenon of stainless steel joints shining?
A simple stainless steel joint is dipped in toothpaste or vinegar with a cotton cloth, and ...
2025-01-07
How is the hardness of stainless steel threaded fittings measured?
Stainless steel threaded fittings are generally measured by three hardness indicators:Brine ...
2025-01-07