Pipe Nipples
Stainless Steel Pipe Nipples
Black Steel Pipe Nipples
Galvanized Pipe Nipples
King Nipples
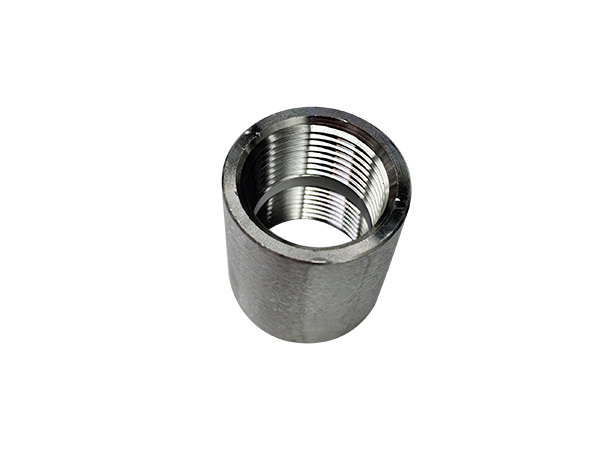
Seamless Threaded Pipe Fittings
The processing technology of seamless threaded pipe fittings mainly includes raw material preparation,pipe blank manufacturing,pipe fitting forming,thread processing,heat treatment,surface treatment,and quality inspection.The following is a detailed introduction for you:
Raw material preparation
Material selection:Choose suitable raw materials based on the requirements and working environment of seamless threaded pipe fittings,commonly including carbon steel,alloy steel,stainless steel,etc.For example,in the petrochemical industry,stainless steel is usually used as the raw material due to the corrosive nature of the medium;In some ordinary mechanical manufacturing fields,carbon steel can meet the demand.
Quality inspection:Conduct strict quality inspection on the purchased raw materials,checking whether the chemical composition,mechanical properties,surface quality,etc.of the materials meet relevant standards and design requirements.Chemical analysis,tensile testing,hardness testing,non-destructive testing,and other methods can be used for inspection.
Pipe blank manufacturing
Hot rolled pipe blank:For larger seamless threaded pipe fittings,hot rolling technology is often used to manufacture pipe blanks.Firstly,heat the steel ingot to a high temperature(usually around 1200℃)to give it good plasticity.Then,the heated steel ingot is pierced into hollow billets through a perforating machine,and then rolled by a pipe rolling machine to reduce the outer diameter and wall thickness of the billets,achieving the required dimensional accuracy and surface quality.
Cold drawn pipe blank:For seamless threaded pipe fittings with high dimensional accuracy and good surface quality requirements,cold drawing technology can be used to manufacture pipe blanks.Cold drawing is the process of drawing hot-rolled billets through a mold at room temperature,further reducing the outer diameter and wall thickness of the billets and improving their dimensional accuracy and surface smoothness.The production efficiency of cold drawn tube blanks is relatively low,but the product quality is high.
Pipe fittings forming
Hot forming:Hot forming is the process of heating a tube blank to a certain temperature(usually between 800-1200℃)to give it good plasticity,and then using a mold for extrusion,forging,or stamping to process the tube blank into the desired shape of a pipe fitting,such as an elbow,tee,reducer,etc.The hot forming process is suitable for manufacturing pipes with complex shapes and large wall thicknesses,which can ensure uniform internal organization of the pipes and improve their strength and toughness.
Cold forming:Cold forming is the process of bending,stretching,and extruding a pipe blank through a mold at room temperature,to process the pipe blank into the desired shape of a pipe fitting.Cold forming technology is suitable for manufacturing pipes with simple shapes and thin wall thicknesses,and has the advantages of high production efficiency,high dimensional accuracy,and good surface quality.However,work hardening occurs during the cold forming process,which increases the hardness and strength of the pipe fittings while reducing their plasticity and toughness.Therefore,subsequent heat treatment is required to eliminate work hardening.
Thread processing
Cutting:Cutting is the most commonly used method for threading,which involves cutting the end of a pipe using threading tools on machine tools such as lathes and milling machines to produce the desired threads.Cutting machining can ensure the accuracy and surface quality of threads,but the production efficiency is relatively low,making it suitable for small batch,high-precision thread machining.
Rolling processing:Rolling processing is the process of rolling the end of a pipe through a rolling die using a rolling machine or a rolling machine,causing plastic deformation of the metal material and forming threads.The production efficiency of rolling processing is high,and the strength and surface quality of the threads are good,but there are certain requirements for the material and hardness of the pipe fittings,which is suitable for large-scale production.
heat treatment
Annealing treatment:Annealing treatment is a heat treatment process in which the pipe fittings are heated to a certain temperature,held for a period of time,and then slowly cooled.Annealing treatment can eliminate residual stresses inside the pipe fittings,reduce hardness,improve plasticity and toughness,and enhance cutting performance.For cold formed pipe fittings,annealing treatment can also eliminate work hardening phenomenon.
Quenching and tempering treatment:Quenching and tempering treatment is a heat treatment process in which the pipe fittings are heated above the critical temperature,held for a period of time,rapidly cooled(quenched),and then heated to a certain temperature,held for a period of time,and then cooled(tempered).Quenching and tempering treatment can improve the strength,hardness,and wear resistance of pipe fittings,and enhance their comprehensive mechanical properties.
surface treatment
Acid pickling and passivation:For seamless threaded stainless steel fittings,acid pickling and passivation treatment are usually required.Acid washing can remove impurities such as oxide scale and rust on the surface of pipe fittings,making the surface of pipe fittings smooth;Passivation can form a dense oxide film on the surface of pipe fittings,improving their corrosion resistance.
Painting or galvanizing:For seamless threaded carbon steel fittings,painting or galvanizing treatment can be carried out.Painting can prevent rusting on the surface of pipe fittings and improve their aesthetic appearance;Galvanizing can form a layer of zinc on the surface of pipe fittings,providing protection and improving their corrosion resistance.
quality testing
Appearance inspection:By visual inspection or using measuring tools,check the appearance quality of the pipe fittings,including dimensional accuracy,surface roughness,surface defects,etc.The surface of the pipe fittings should be smooth,free of cracks,sand holes,scratches and other defects,and the size should meet the design requirements.
Non destructive testing:Non destructive testing methods such as ultrasonic testing,magnetic particle testing,and radiographic testing are used to inspect for defects such as cracks,pores,and slag inclusions inside the pipe fittings.Non destructive testing can detect internal defects in pipes without damaging them,ensuring the quality of the pipes.
Mechanical performance testing:Conduct mechanical performance testing on pipe fittings,such as tensile testing,hardness testing,impact testing,etc.,to check whether the mechanical performance of pipe fittings meets relevant standards and design requirements.Mechanical performance testing can evaluate performance indicators such as strength,toughness,and hardness of pipe fittings.
What should I do if the stainless steel joint leaks?
Stainless steel joints are a common type of pipeline connection,which are widely used in in ...
2025-01-07
Several common problems in the use of stainless steel joints
With the continuous development of stainless steel joint technology and enterprises, stainl ...
2025-01-07
How to deal with the phenomenon of stainless steel joints shining?
A simple stainless steel joint is dipped in toothpaste or vinegar with a cotton cloth, and ...
2025-01-07
How is the hardness of stainless steel threaded fittings measured?
Stainless steel threaded fittings are generally measured by three hardness indicators:Brine ...
2025-01-07