Pipe Nipples
Stainless Steel Pipe Nipples
Black Steel Pipe Nipples
Galvanized Pipe Nipples
King Nipples
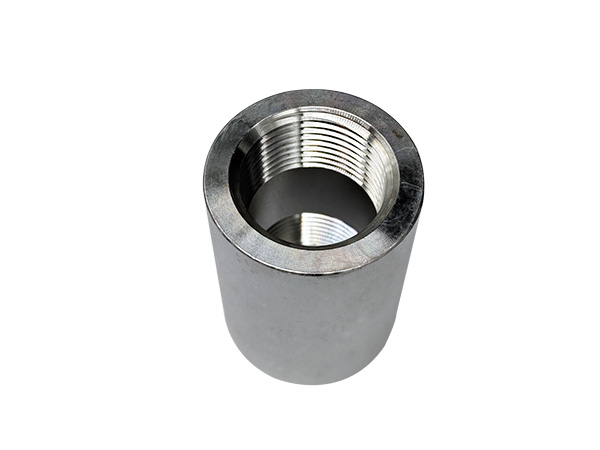
Seamless Threaded Pipe Fittings
The operation of welding seamless threaded pipe fittings requires comprehensive consideration of multiple aspects to ensure welding quality and safety. The following are detailed precautions:
Preparation before welding
Material inspection
Confirm that the materials,specifications,and design requirements of the pipe fittings and welding materials are consistent.For example,when welding stainless steel fittings,it is necessary to ensure that the welding rod or wire is also made of stainless steel material and matches the model.
Check if there are any quality issues with the pipe fittings and welding materials,such as no cracks or sand holes on the surface of the pipe fittings,and the welding materials should not be affected by moisture or deterioration.
Pipe cleaning
Thoroughly remove impurities such as rust,oil,moisture,and oxide scale from the welding area of the pipe fittings and its surrounding areas.Mechanical cleaning can be carried out using tools such as sandpaper and wire brushes,and then wiped clean with organic solvents such as acetone to ensure good fusion during welding and avoid defects such as porosity and slag inclusion.
Groove processing
Process suitable grooves according to the thickness of the pipe fittings and welding requirements.Common groove forms include V-shaped,U-shaped,X-shaped,etc.The size and angle of the groove should comply with relevant standards or design requirements to ensure the penetration and strength of the weld seam.
The surface of the processed groove should be smooth and free of defects such as cracks and delamination,and tools such as angle grinders should be used to polish a certain range on both sides of the groove until a metallic luster is exposed.
Debugging of welding equipment
Debug welding equipment to ensure its normal performance.Reasonably set welding current,voltage,welding speed and other parameters based on welding process,pipe material,thickness and other parameters.For example,when welding thicker pipe fittings,a larger welding current is required;When welding stainless steel fittings,it is necessary to control the welding heat input.
welding process
safety protection
Operators must wear appropriate protective equipment,such as welding masks,protective gloves,protective clothing,etc.,to prevent injuries such as arc radiation and splash burns.
The welding site should maintain good ventilation conditions to eliminate harmful gases and smoke generated during the welding process and ensure the health of operators.
Welding operation
Arc striking:When manually arc welding,avoid striking the arc randomly on the surface of the pipe to prevent damage to the surface of the pipe.When starting the arc in gas shielded welding,it is necessary to ensure that the shielding gas is delivered in advance to eliminate the air in the welding area.
Welding speed:Maintain an appropriate welding speed,as excessive speed may lead to defects such as poor fusion and porosity in the weld seam;If the speed is too slow,it will cause the weld seam to widen and the deformation to increase.The welding speed should be adjusted according to the welding process parameters and weld requirements.
Welding layers:For thicker pipe fittings,multi-layer and multi pass welding is required.The thickness of each weld seam should not be too thick,generally controlled at 3-5mm.After each layer of welding is completed,the welding slag should be cleaned up in a timely manner,and the quality of the weld seam should be checked.If there are defects,they should be dealt with in a timely manner before proceeding to the next layer of welding.
Swinging method:According to the width and requirements of the weld seam,use appropriate swinging methods such as straight line,crescent,sawtooth,etc.The swing amplitude should be uniform to ensure consistent weld width and good fusion.
Special case handling
If welding rod sticking or unstable arc occurs during the welding process,welding should be stopped immediately,the cause should be identified,and corresponding measures should be taken to solve the problem before continuing welding.
When encountering windy environments,windproof measures should be taken for gas shielded welding,such as setting up windproof shelters or using windproof plates,to ensure the protective effect of the protective gas and prevent defects such as porosity in the weld seam.
Post weld treatment
Weld cleaning
After welding,use tools such as slag hammers and wire brushes to clean the surface of the weld seam of impurities such as welding slag and spatter,making the surface of the weld seam flat and smooth.
Weld inspection
Appearance inspection:Check whether there are cracks,pores,slag inclusions,undercutting and other defects on the surface of the weld seam,and whether the dimensions of the weld seam such as excess height and width meet the requirements.
Non destructive testing:According to design requirements and relevant standards,non-destructive testing is carried out on welds,such as ultrasonic testing(UT),radiographic testing(RT),magnetic particle testing(MT),penetrant testing(PT),etc.,to detect whether there are defects inside the weld.
Heat treatment(optional)
For some pipe fittings that require high mechanical properties of the weld seam,post weld heat treatment may be necessary,such as annealing,normalizing,tempering,etc.Heat treatment can eliminate residual stresses in welding,improve the microstructure and properties of welds and heat affected zones.The heat treatment process parameters should be determined based on the material of the pipe fittings and design requirements.
Thread protection
During the welding process,attention should be paid to protecting the threaded part of the pipe fittings.Thread protection sleeves can be used to prevent welding spatter from damaging the threads and affecting the subsequent connection and sealing performance.
Production process of seamless threaded pipe fittings
The production of seamless threaded pipe fittings requires multiple stages,each of which has an impact on the final quality of the fittings.The following is a detailed introduction:
Raw material selection and inspection
Material selection:Select suitable seamless pipes based on the usage scenario,pressure level,medium characteristics,and other factors of the pipe fittings.For example,carbon steel seamless pipes can be used for ordinary water and gas transportation;For occasions with corrosion resistance requirements,such as the chemical industry,stainless steel seamless pipes can be used;Copper seamless pipes can be used in places where thermal conductivity is required,such as air conditioning refrigeration systems.
Material inspection:Strictly inspect the purchased seamless pipes,including visual inspection,to check for defects such as cracks,sand holes,scratches,etc.on the surface of the pipes;Measure the dimensions to ensure that the pipe diameter,wall thickness,etc.meet the standard requirements;And conduct chemical composition analysis and mechanical property testing to ensure that the quality and performance of the material meet the standards.
Cutting and cutting materials
Determining dimensions:Based on the design specifications and usage requirements of the pipe fittings,accurately calculate and determine the required length of the pipe material.
Cutting operation:Use appropriate cutting equipment and methods for cutting.For pipes with smaller diameters,sawing machines can be used for cutting,with smooth and high-precision cuts;For pipes with larger diameters,flame cutting or plasma cutting can be used,but after cutting,the incision needs to be polished to remove oxide skin and burrs,ensuring the quality of the incision.
Thread processing
Process selection:Select the appropriate thread processing technology based on the size,precision requirements,and production batch of the pipe fittings.Common methods include cutting and rolling processing.Cutting processing is suitable for thread machining with various precision requirements and can be carried out on equipment such as lathes and thread machining centers;Rolling processing has high production efficiency,good thread strength,and is suitable for large-scale production.
Thread specification control:Strictly process threads according to design requirements to ensure that the dimensional accuracy of thread profile,pitch,outer diameter,inner diameter,etc.meets the standards.During the processing,it is necessary to regularly use thread gauges for inspection,adjust processing parameters in a timely manner,and ensure thread quality.
Forming processing
Bending Forming:For elbow fittings,processes such as hot bending,cold bending,or pushing can be used.Hot bending is the process of heating pipes to a certain temperature and then bending them,suitable for large diameter and thick walled pipes;Cold bending is carried out at room temperature,which is relatively simple to operate,but requires high requirements for the material and performance of the pipe;Pushing elbows are made by using a dedicated pushing machine to push pipes into the desired bending angle in a mold.
Three way and four-way forming:The forming methods of three-way and four-way pipe fittings include hydraulic bulging,hot extrusion,etc.Hydraulic bulging is the process of using liquid pressure to expand and shape pipes in a mold;Hot extrusion is the process of extruding heated pipes into a tee or four-way shape through a mold.
Welding(if applicable)
Preparation before welding:For the pipe fittings that need to be welded,the welding area should be cleaned before welding to remove impurities such as oil and rust,and groove processing should be carried out to ensure welding quality.Meanwhile,select appropriate welding materials and welding processes based on the material of the pipe fittings.
Welding operation:Strictly follow the welding process,control the welding current,voltage,welding speed and other parameters to ensure the depth,width and forming quality of the weld seam.During the welding process,attention should be paid to preventing the occurrence of defects such as porosity,slag inclusion,and cracks.
Post weld treatment:Clean and inspect the weld seam after welding,and perform heat treatment if necessary to eliminate welding stress and improve the structure and properties of the weld seam.
heat treatment
Purpose:Heat treatment can improve the mechanical properties of pipe fittings,eliminate residual stresses generated during processing,and enhance the strength,toughness,and corrosion resistance of pipe fittings.
Process selection:Select the appropriate heat treatment process based on the material and performance requirements of the pipe fittings,such as annealing,normalizing,quenching,tempering,etc.For example,carbon steel seamless fittings are often annealed to reduce hardness and improve cutting performance;Stainless steel fittings may require solution treatment to improve corrosion resistance.
surface treatment
Rust removal:Shot blasting,sandblasting and other methods are used to remove the oxide scale and rust on the surface of the pipe fittings,making the surface of the pipe fittings appear metallic luster,improving surface quality and coating adhesion.
Anti corrosion treatment:According to the usage environment and requirements of the pipe fittings,anti-corrosion treatment is carried out on the surface of the pipe fittings,such as painting,galvanizing,spraying anti-corrosion coatings,etc.Anti corrosion treatment can extend the service life of pipe fittings and prevent rusting and corrosion during use.
quality testing
Appearance inspection:By visual inspection or using tools such as magnifying glasses,check whether there are cracks,sand holes,pores,burrs,and other defects on the surface of the pipe fittings,as well as whether the appearance quality of the weld meets the requirements.
Dimensional measurement:Use measuring tools to measure the diameter,wall thickness,length,thread size,etc.of the pipe fittings to ensure that the dimensional accuracy of the pipe fittings meets the design requirements.
Non destructive testing:Ultrasonic testing,radiographic testing,magnetic particle testing and other non-destructive testing methods are used to detect whether there are cracks,lack of penetration and other defects inside the pipe fittings.
Pressure test:Conduct a pressure test on the pipe fittings to check whether their pressure resistance and sealing performance are good.The test pressure and time should comply with relevant standards and design requirements.
What should I do if the stainless steel joint leaks?
Stainless steel joints are a common type of pipeline connection,which are widely used in in ...
2025-01-07
Several common problems in the use of stainless steel joints
With the continuous development of stainless steel joint technology and enterprises, stainl ...
2025-01-07
How to deal with the phenomenon of stainless steel joints shining?
A simple stainless steel joint is dipped in toothpaste or vinegar with a cotton cloth, and ...
2025-01-07
How is the hardness of stainless steel threaded fittings measured?
Stainless steel threaded fittings are generally measured by three hardness indicators:Brine ...
2025-01-07