Pipe Nipples
Stainless Steel Pipe Nipples
Black Steel Pipe Nipples
Galvanized Pipe Nipples
King Nipples
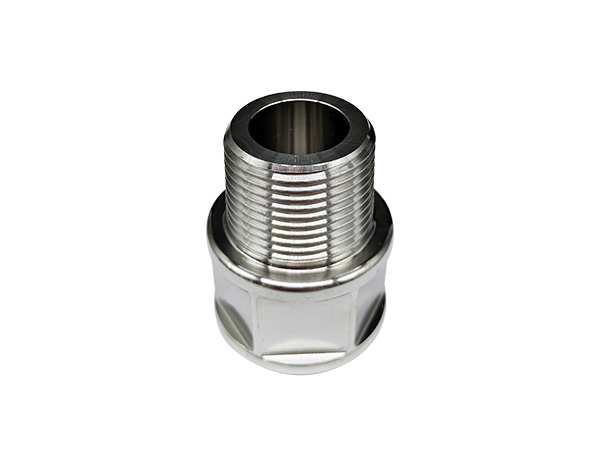
Welded Threaded Pipe Fittings
Welding threaded pipe fittings requires comprehensive consideration of multiple aspects to ensure welding quality and safety.The following are detailed points to note:
Preparation before welding
Material inspection
Confirm that the materials,specifications,and design requirements of the pipe fittings and welding materials are consistent.For example,when welding stainless steel fittings,it is necessary to ensure that the welding rod or wire is also made of stainless steel material and matches the model.
Check if there are any quality issues with the pipe fittings and welding materials,such as no cracks or sand holes on the surface of the pipe fittings,and the welding materials should not be affected by moisture or deterioration.
Pipe cleaning
Thoroughly remove impurities such as rust,oil,moisture,and oxide scale from the welding area of the pipe fittings and its surrounding areas.Mechanical cleaning can be carried out using tools such as sandpaper and wire brushes,and then wiped clean with organic solvents such as acetone to ensure good fusion during welding and avoid defects such as porosity and slag inclusion.
Groove processing
Process suitable grooves according to the thickness of the pipe fittings and welding requirements.Common groove forms include V-shaped,U-shaped,X-shaped,etc.The size and angle of the groove should comply with relevant standards or design requirements to ensure the penetration and strength of the weld seam.
The surface of the processed groove should be smooth and free of defects such as cracks and delamination,and tools such as angle grinders should be used to polish a certain range on both sides of the groove until a metallic luster is exposed.
Debugging of welding equipment
Debug welding equipment to ensure its normal performance.Reasonably set welding current,voltage,welding speed and other parameters based on welding process,pipe material,thickness and other parameters.For example,when welding thicker pipe fittings,a larger welding current is required;When welding stainless steel fittings,it is necessary to control the welding heat input.
welding process
safety protection
Operators must wear appropriate protective equipment,such as welding masks,protective gloves,protective clothing,etc.,to prevent injuries such as arc radiation and splash burns.
The welding site should maintain good ventilation conditions to eliminate harmful gases and smoke generated during the welding process and ensure the health of operators.
Welding operation
Arc striking:When manually arc welding,avoid striking the arc randomly on the surface of the pipe to prevent damage to the surface of the pipe.When starting the arc in gas shielded welding,it is necessary to ensure that the shielding gas is delivered in advance to eliminate the air in the welding area.
Welding speed:Maintain an appropriate welding speed,as excessive speed may lead to defects such as poor fusion and porosity in the weld seam;If the speed is too slow,it will cause the weld seam to widen and the deformation to increase.The welding speed should be adjusted according to the welding process parameters and weld requirements.
Welding layers:For thicker pipe fittings,multi-layer and multi pass welding is required.The thickness of each weld seam should not be too thick,generally controlled at 3-5mm.After each layer of welding is completed,the welding slag should be cleaned up in a timely manner,and the quality of the weld seam should be checked.If there are defects,they should be dealt with in a timely manner before proceeding to the next layer of welding.
Swinging method:According to the width and requirements of the weld seam,use appropriate swinging methods such as straight line,crescent,sawtooth,etc.The swing amplitude should be uniform to ensure consistent weld width and good fusion.
Special case handling
If welding rod sticking or unstable arc occurs during the welding process,welding should be stopped immediately,the cause should be identified,and corresponding measures should be taken to solve the problem before continuing welding.
When encountering windy environments,windproof measures should be taken for gas shielded welding,such as setting up windproof shelters or using windproof plates,to ensure the protective effect of the protective gas and prevent defects such as porosity in the weld seam.
Post weld treatment
Weld cleaning
After welding,use tools such as slag hammers and wire brushes to clean the surface of the weld seam of impurities such as welding slag and spatter,making the surface of the weld seam flat and smooth.
Weld inspection
Appearance inspection:Check whether there are cracks,pores,slag inclusions,undercutting and other defects on the surface of the weld seam,and whether the dimensions of the weld seam such as excess height and width meet the requirements.
Non destructive testing:According to design requirements and relevant standards,non-destructive testing is carried out on welds,such as ultrasonic testing(UT),radiographic testing(RT),magnetic particle testing(MT),penetrant testing(PT),etc.,to detect whether there are defects inside the weld.
Heat treatment(optional)
For some pipe fittings that require high mechanical properties of the weld seam,post weld heat treatment may be necessary,such as annealing,normalizing,tempering,etc.Heat treatment can eliminate residual stresses in welding,improve the microstructure and properties of welds and heat affected zones.The heat treatment process parameters should be determined based on the material of the pipe fittings and design requirements.
Thread protection
During the welding process,attention should be paid to protecting the threaded part of the pipe fittings.Thread protection sleeves can be used to prevent welding spatter from damaging the threads and affecting the subsequent connection and sealing performance.
What should I do if the stainless steel joint leaks?
Stainless steel joints are a common type of pipeline connection,which are widely used in in ...
2025-01-07
Several common problems in the use of stainless steel joints
With the continuous development of stainless steel joint technology and enterprises, stainl ...
2025-01-07
How to deal with the phenomenon of stainless steel joints shining?
A simple stainless steel joint is dipped in toothpaste or vinegar with a cotton cloth, and ...
2025-01-07
How is the hardness of stainless steel threaded fittings measured?
Stainless steel threaded fittings are generally measured by three hardness indicators:Brine ...
2025-01-07