Pipe Nipples
Stainless Steel Pipe Nipples
Black Steel Pipe Nipples
Galvanized Pipe Nipples
King Nipples
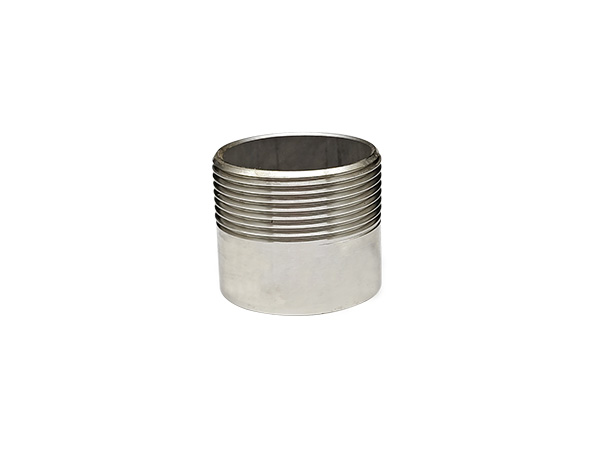
Welded Threaded Pipe Fittings
When Welded Threaded Pipe Fittings made of different materials,there are differences in the key points that need to be noted due to the different material characteristics.The following are the precautions for welding seamless threaded fittings made of several common materials:
Carbon steel seamless threaded pipe fittings
Preparation before welding
Cleaning:Thoroughly remove impurities such as rust,oil stains,and moisture from the welding parts of the pipe fittings to prevent defects such as porosity and slag inclusion during the welding process.Mechanical cleaning can be carried out using tools such as sandpaper and wire brushes,and then wiped clean with organic solvents such as acetone.
Preheating(depending on the situation):For carbon steel pipe fittings with large thickness or high carbon content,preheating is required before welding to reduce welding stress and avoid cracking.The preheating temperature is generally between 100-200℃,and the specific temperature should be determined according to the material and thickness of the pipe fittings.
Electrode selection:Choose the appropriate electrode based on the composition and properties of carbon steel.In general,E43 series or E50 series welding rods can be used,such as E4303,E5015,etc.Welding rods should be dried according to regulations before use to remove moisture from the welding rods.
welding process
Welding parameter control:Reasonably select welding current,voltage,and welding speed.Excessive welding current can easily lead to problems such as undercutting and burning through of the weld seam,while insufficient current can result in defects such as incomplete penetration and poor fusion.The welding speed should be moderate to ensure the quality of the weld formation.
Welding sequence:For multi pass welding,attention should be paid to the welding sequence to avoid excessive welding stress.Generally,methods such as segmented back welding and symmetrical welding are used to reduce the deformation of the weld seam.
Interlayer cleaning:When welding multiple layers,the welding slag and spatter should be cleaned up in a timely manner after each layer is welded,and the surface of the weld should be checked for defects.If there are defects,they should be dealt with in a timely manner before proceeding to the next layer of welding.
Post weld treatment
Stress relief treatment(optional):For fittings that bear large loads or require high welding quality,stress relief annealing treatment can be performed after welding to reduce residual welding stress and improve the service life of the fittings.The annealing temperature is generally between 600-650℃,and after holding for a certain period of time,it is slowly cooled.
Appearance inspection:After welding,conduct a visual inspection of the weld seam to check whether the excess height,width,surface flatness,etc.of the weld seam meet the requirements.The surface of the weld seam must not have defects such as cracks,pores,slag inclusions,etc.
Stainless steel seamless threaded pipe fittings
Preparation before welding
Cleaning:Impurities such as grease and oxide scale on the surface of stainless steel fittings can affect welding quality,so strict cleaning is necessary.Special stainless steel cleaner or acetone can be used for cleaning,and then wiped dry with a clean cloth.After cleaning,avoid contaminating the welding area again.
Preventing carburization:During the welding process,it is necessary to prevent surface carburization of stainless steel fittings to avoid reducing their corrosion resistance.The welding site should be kept clean and avoid contact with materials such as carbon steel that are prone to carburization.
Selection of welding rod or wire:Choose the appropriate welding rod or wire based on the material and usage requirements of stainless steel.For example,for 304 stainless steel fittings,welding rods of models such as E308-16 and E308-17 can be used;For 316 stainless steel fittings,welding rods of models such as E316-16 and E316-17 can be used.The selection of welding wire should also match the base material.
welding process
Control welding heat input:Stainless steel has poor thermal conductivity and is prone to overheating during welding,resulting in coarse grain size in the weld seam and reduced corrosion resistance and mechanical properties.Therefore,it is necessary to strictly control the welding heat input and adopt low current and fast welding methods to reduce the residence time of the weld at high temperatures.
Protective gas:When using gas shielded welding,appropriate protective gas should be selected.For stainless steel welding,the commonly used shielding gas is argon gas,with a purity of not less than 90%,to ensure the quality and surface color of the weld seam.
Preventing intergranular corrosion:During the welding process,it is necessary to avoid staying in the sensitization temperature range of 450-850℃for too long to prevent intergranular corrosion.Appropriate welding processes and post weld heat treatment can be used to prevent intergranular corrosion from occurring.
Post weld treatment
Acid pickling and passivation:After welding,the weld seam is subjected to acid pickling and passivation treatment to remove the oxide scale and impurities on the surface of the weld seam and restore the corrosion resistance of stainless steel.Acid washing and passivation can be carried out by chemical or mechanical methods.
Appearance inspection and non-destructive testing:Conduct a visual inspection of the weld seam after welding to check for defects such as cracks,porosity,and undercutting on the surface of the weld seam.At the same time,non-destructive testing such as radiographic testing,ultrasonic testing,etc.shall be conducted as required to ensure that the internal quality of the weld meets the standards.
Alloy steel seamless threaded pipe fittings
Preparation before welding
Preheating:Alloy steel pipe fittings generally require strict preheating treatment,and the preheating temperature should be determined according to the composition of the alloy steel and the thickness of the pipe fittings.Preheating can reduce the cooling rate of welding and prevent the formation of cold cracks.The preheating range should include the welding area and a certain width area on both sides.
Selection of welding rods or wires:Choose welding rods or wires that match the composition and properties of the base material based on the type and properties of the alloy steel.At the same time,attention should be paid to the baking and storage conditions of welding rods or wires to prevent moisture and deterioration.
Groove processing:The groove processing of alloy steel pipe fittings should ensure dimensional accuracy and surface quality.The groove surface should be flat,free of cracks,oxygen scale and other defects.After processing,the groove should be cleaned and polished to ensure welding quality.
welding process
Welding parameter control:The welding parameters of alloy steel need to be strictly controlled,and the welding current,voltage,and welding speed should be reasonably selected based on factors such as the material,thickness,and welding position of the pipe fittings.During the welding process,it is necessary to maintain the stability of welding parameters to avoid welding defects.
Interlayer temperature control:When welding multiple layers,the interlayer temperature should be controlled well,and it should not be lower than the preheating temperature to prevent the occurrence of cold cracks.Meanwhile,the interlayer temperature should not be too high to avoid affecting the performance of the weld seam.
Post heat treatment(if necessary):For some alloy steel pipe fittings that are prone to delayed cracking,post heat treatment is required after welding.The post heating temperature is generally between 200-350℃,and the insulation time is determined according to the thickness and material of the pipe fittings.Post heating can accelerate the escape of hydrogen from the weld and reduce residual stresses in the weld.
Post weld treatment
Heat treatment:Alloy steel pipe fittings usually require heat treatment after welding to improve the microstructure and properties of the weld seam and heat affected zone,and eliminate welding residual stresses.The heat treatment process includes annealing,normalizing,tempering,etc.,and the specific process should be determined according to the type and usage requirements of the alloy steel.
Non destructive testing:Comprehensive non-destructive testing is performed on the weld seam after welding,such as ultrasonic testing,radiographic testing,magnetic particle testing,etc.,to check for defects such as cracks and incomplete penetration inside the weld seam.Only after passing the inspection can the next step of installation and use be carried out.
What should I do if the stainless steel joint leaks?
Stainless steel joints are a common type of pipeline connection,which are widely used in in ...
2025-01-07
Several common problems in the use of stainless steel joints
With the continuous development of stainless steel joint technology and enterprises, stainl ...
2025-01-07
How to deal with the phenomenon of stainless steel joints shining?
A simple stainless steel joint is dipped in toothpaste or vinegar with a cotton cloth, and ...
2025-01-07
How is the hardness of stainless steel threaded fittings measured?
Stainless steel threaded fittings are generally measured by three hardness indicators:Brine ...
2025-01-07